Job Shop Fabrication for Specialty Engine-Driven Equipment
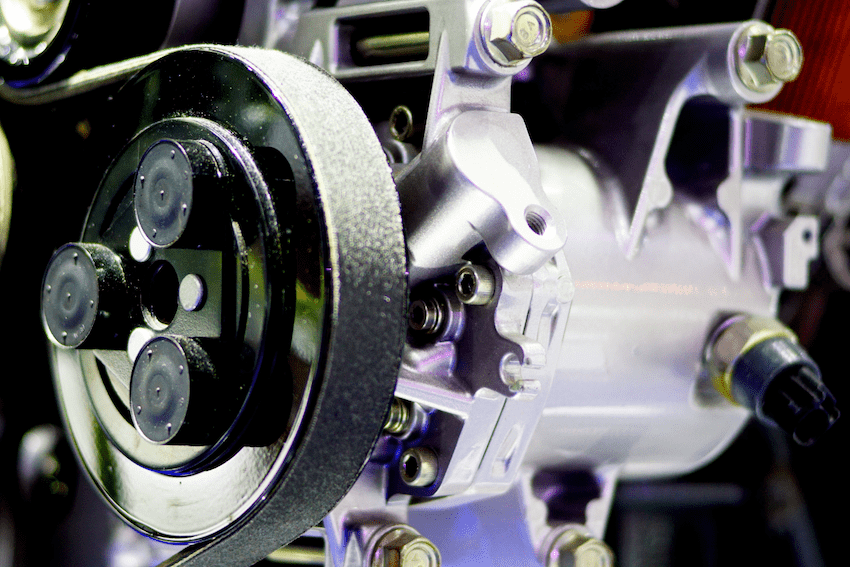
Custom Fabrication for Engine-Driven Equipment
As a nationwide builder of engine heat transfer components, we see a huge amount of unique, highly specialized equipment projects firsthand. System designers are constantly trying to satisfy multiple interests all at once - namely regarding performance, emissions compliance, and cost. In the world of Tier 3 and 4 diesel equipment especially, there are very few components involved that would be off-the-shelf, which calls for custom fabrication to achieve the designers' vision. Custom fabrication of this nature is best performed by job shops – these are manufacturing and fabrication facilities that can tackle entire projects or ‘jobs’, not being bound by a singular function or skillset. In this article, we'll explain key job shop fabrication techniques that help solve custom project challenges, and then share insight into how your equipment fleet can benefit from engaging custom fabrication support.
To set the stage, let’s pose a question: where might the opportunity to engage a job shop come up in your everyday fleet operations? Typically, when you need support with either:
- New Projects – you’re working on a new system design, vehicle retrofit, or performance upgrade, and are considering what resources you need to fabricate, assemble, and install components.
- Equipment Service – you have an existing vehicle or equipment piece that needs routine maintenance or emergency repairs, and are considering what resources you need to perform the necessary work to get you back into operation.
Job Shop Processes and their Applications
A competent job shop utilizes a wide array of tool processes operated by trained, experienced craftspersons to complete its projects, including:
Computer-Aided Design
Modern fab shops start all component projects with detailed 2D and 3D computer-aided design (CAD) software. Within CAD programs, designers can test out fabrication processes, analyze design alternatives, optimize for waste and yields, and quantify exact costs, all in a digital environment. Designs can be further developed using advanced thermal, structural, hydraulic, emissions, and efficiency modeling software.
Cutting and Patterning
Many components are made from flat sheet or plate materials, which can be cut down to size and shape with automatic laser and plasma cutters. Laser and plasma cutters are especially useful for creating patterns and features in a single process, such as holes, channels, slots, and knockouts. Laser cutters are extremely accurate and used on final cuts through thinner sheet metals, while plasma cutters are less precise and used on rough cuts through thicker plates and structural shapes.
Shearing and Forming
When needing a straight cut through thick materials, a hydraulic shear works wonders and is faster than setting up a plasma cut. Hydraulic shears and ironworkers can generate thousands of pounds of force to cleanly slice, notch, punch, and nibble steel plates. Once plates or sheets are cut to size, they can be further shaped with hydraulic rollers and press brakes into cylinders, cones, rings, tubes, channels, boxes, and other formed shapes.
Welding and Joining
Joining separate metal components together is commonly achieved through either bolting, pressing, or welding. Each option must be done with precise care and technical consideration, as joints tend to be the most common failure points for fabricated components. Drilling and tapping threads requires accurate alignment and thread depth, while pressing calls for specific friction-fit tolerances and press pressures. MIG and TIG welding is most common for critical structural and thermal components, fusing metals together under extreme heat and requiring strict procedures to avoid weld failures.
CNC Machining
Computer Numerical Control (CNC) machining is an automated milling process that uses computer-generated instruction code to control complex, high precision tool work. CNC machines typically begin work on a raw material shape, and by removing material one thin layer at a time, will produce a finished shape complete with various features and finishes that would have otherwise taken multiple manual tool processes and much more time.
Finishing and Cleaning
In the context of metal fabrication, finishing refers to a tool process that will bring a part's surface down to the desired final tolerance and appearance. Surface buffing, burnishing, polishing, and blending are good examples. Heat treatment is another finishing option that strengthens materials by influencing their molecular structures. Chemical treatments such as passivation and electroplating serve to protect the component's surface. Finally, rinsing, disinfection, degreasing, and caustic cleaning all help remove potential contaminants and residues left over from fabrication.
Benefits for Equipment Builders and Owners
When engaging a job shop for custom fabrication, vehicle repairs, or equipment modifications, readers should evaluate options and select a resource based on these benefits:
- Coordinated Fabrication with Fewer Players – using a job shop to consolidate fabrication processes, as opposed to managing multiple fabricators and suppliers working separately, provides much more consistency and control over design details, costs, and schedule.
- Greater Quality Control – completing a fabrication project in a singular environment, with all work processes audited and controlled in a shared shop environment, drives a higher level of quality control over the finished product.
- Heightened Compliance and Standardization – turning to a single job shop reduces the amount of variation you’ll receive in a finished project, where common hardware, accessories, finishes, documentation, and traceability can be provided.
- Faster Execution and Turn-Around – job shops can move quickly, having all of the necessary engineering, tooling, and experience under one roof that it takes to knock out an integrated fabrication project.
- Combining Value-Added Services - very often, job shops offer additional value-added services that can be performed simultaneously with a defined project, getting more work done at once, often at a price advantage. Multi-service job shops will each have their own specialties, such as the below offered here at CR:
- Diesel Fuel Tank Fabrication including Supports, Nozzles, and Installation
- Custom Heat Exchangers complete with Mounting Frame, Reservoir, and Fan Brackets
- Diesel Particulate Filter Cleaning and Replacement
- Instrument Assemblies including custom Pressure, Vacuum, Temperature, and Level Sensors
- Fuel Tank Reconditioning, Pressure Testing, and Painting
Mission-critical vehicles and equipment in over a dozen infrastructure sectors rely on heat transfer components manufactured by Cincinnati Radiator. CR works directly with Original Equipment Manufacturers and Aftermarket service channels to supply premium-grade, long life radiators, coolers, and full cooling packages into extreme applications all over the world. With our expanding inventory and fabrication space at our Fairfield, Ohio facility, we pride ourselves on having a personal touch, ultra-fast lead times, and one-off custom design capabilities.
For your next vehicle or heavy equipment heat transfer project, call us at (513) 874-5555, email us at sarslan@cincyradiator.com, or visit our website at https://cincyradiator.com/