Comparing Fin Designs in Heavy-Duty Radiators
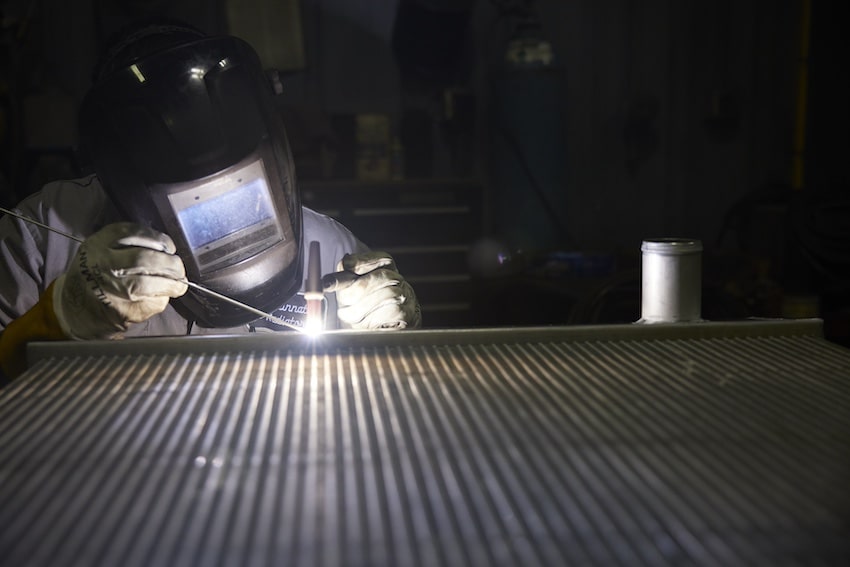
Air-Cooled Radiators - Cooling Engines One Square Inch at a Time
Internal combustion engines touch our daily lives in more ways than we tend to recognize. From motor vehicles to electrical generators, industrial equipment, emergency backup systems, and so on; we may not always see them in use, but we highly depend upon them, nonetheless. Engines of all types have to expel their waste heat in order to operate, with most engines relying on a single component to do so: an air-to-liquid heat exchanger, more commonly known as a radiator or jacketwater (JW). A radiator’s ability to keep engines cool is heavily dependent on its fin design, bringing us to the topic of this article – radiator fins and their common designs, selection criteria, and associated application considerations.
Within each radiator, coolant flows through many thin-walled tubes which conduct heat away from the coolant and across thin aluminum or copper sheet metal fins attached around the tubes. Outside air is pushed over these fins by a fan (as well as by physical motion, in the case of vehicle radiators), and this air extracts the heat from the fins, dissipating it into the atmosphere.
From the above, we can see that radiator fins serve three distinct functions:
- As a heat sink for heat energy that is conducted out of the engine's liquid coolant, and
- As heat transfer surface area, from which flowing air can pick up and remove that heat energy
- As a vital component of the radiator’s structure in combination with the tubes
When designing radiators, fin details and engineering decisions track directly against the above two functions. In most cases, designers want to maximize surface area so as to get more contact with flowing air where heat transfer can occur. Increased surface area naturally requires more sheet metal fin material overall, which adds heat sink mass as well. All in all, designers select fin designs to best match the application’s technical requirements, such as surface area, airflow rate, airflow resistance, tolerance to clogging, and overall cooling performance.
Comparing Radiator Fin Designs
Next we’ll showcase the three most common radiator fin designs used in industrial vehicles and equipment today, explaining their features and benefits along the way.
Plain Fins
A Plain Fin design consists of a stamped rectangular pattern that provides large, continuous, straight channels for air to flow through. Each channel has square corners and straight sidewalls, maximizing the channel width and clearance. Plain fins present low pressure drop for increased mass airflow, great for dirty environments where heavy airborne contaminants would clog lower clearance fin designs. In fact, the higher airflow velocity achievable with plain fins serves in part as a self-cleaning feature. Plain fins can also include louvered sidewalls which generate more turbulence and thermal exchange, as pictured to the left.
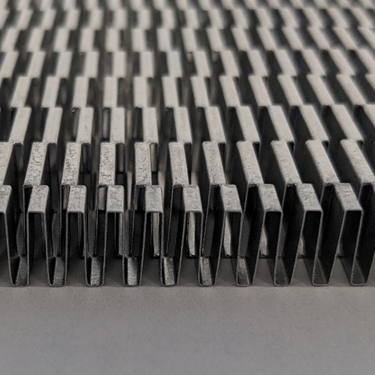
Offset Fins
An Offset Fin design breaks the continuous channel concept of Plain Fins into rows of slightly unaligned (or offset) channels. This offset profile breaks up airflow, creating turbulence and adding surface area that together improve the radiator’s heat transfer capacity. Offset fin radiators prefer to operate in cleaner environments, as the small annular spaces created between channel edges are more sensitive to clogging. That said, offset fins offer increased cooling potential in a smaller footprint, making them the ideal candidate for high performance applications.
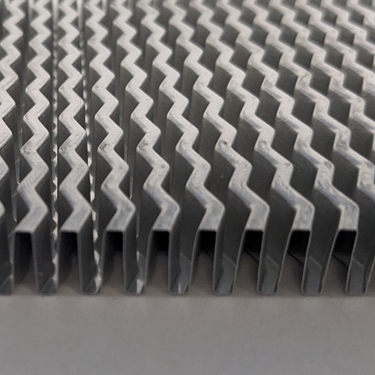
Wavy Fins
As a mid-point between Plain and Offset fin profiles, Wavy Fin profiles combine the concept of straight plain fins with a mild undulation down channel paths. This wavy profile is less restrictive to airflow than offset fins, but still increases surface area and adds beneficial turbulence over plain fin designs. Wavy fin designs are great for high pressure, high heat transfer application where there is a mild risk of clogging such as in industrial hydraulic systems.
----
Aside from the above three fin designs, there are additional options available on the market. Louvered fins, pin fins, stacked plate fins, corrugated fins, and even honeycomb fins are some of the options available for very unique or technical applications. In all cases, these additional options are variations of the above three main profiles, and should be selected only if deemed necessary through detailed engineering design review.
Application Considerations
Aside from fin design, there are several other important factors that altogether determine how a radiator will thermally perform. Buyers should include these details in their review of OEM and aftermarket radiator options, striving to end up with the best possible solution for their specific use case.
- Coolant Properties - engine coolant is made up of glycol-based antifreeze chemicals and water. As different proportions and chemistries of coolant perform differently across varying applications, it's also the case that different chemistries can align with particular radiator design features to drive higher performance. For example, a higher boiling point mixture suited for extreme-temperature applications will benefit from the high heat transfer potential of offset tube fins over straight fins.
- Radiator Material - a radiator's ability to dispel heat significantly relies on the thermal conductivity potential of the materials making up the radiator. Thick radiator tubes made of very dense material do not transfer as much heat to the fins as would thin, low-density radiator tubes, resulting in poor thermal efficiency. For this reason, aluminum tubes and fins are usually preferred for their high heat transfer rates and best cost-value. Copper/Bronze materials offer higher thermal conductivity, but tend to be more costly, much heavier, and more susceptible to wear. Steel materials are a third choice, usually selected for low cost, but are much more prone to corrosion.
- Airflow Rate and Pressure - most vehicle and engine radiators today are equipped with forced-air fans to drive air across the radiator fins in a semi-controlled manner. This relatively consistent velocity and pressure present the radiator with a minimum flow of air mass to draw heat out of the coolant, which would only increase in moving vehicles and remain static in fixed equipment. Fin designs (specifically, their surface area and turbulence factors) are designed explicitly against this airflow rate and pressure profile, which should all be considered together when selecting a radiator design.
- Ambient Conditions - the hotter it is outside, the less effective a radiator is at dispelling heat from its coolant. On top of this, higher humidity, direct sun exposure, and high-altitude elevation (as related to atmospheric pressure) are all ambient conditions that impact a radiator's performance. This is not to say that low temperatures are automatically better, as sub-freezing temperatures may require more robust radiator designs to accommodate the thermal expansion that will occur each initial heat-up, which works against thermal conduction. Radiator design and selection must take all of these factors into account.
- Radiator Health - as radiators age, their performance tends to decline due to internal corrosion and fouling, external buildup and scale, fin damage, tube restriction, and other wear and tear. When initially designing a radiator, engineers try to include normal aging rates in their calculations, so that the radiator can tolerate these natural declines in performance. For applications that may see aggressive use or excessive wear and tear, buyers should notify their radiator supplier so as to select a radiator design up front that will offer a reasonable mix of cost, performance, and lifespan.
Mission-critical vehicles and equipment in over a dozen infrastructure sectors rely on heat transfer components manufactured by Cincinnati Radiator. CR works directly with Original Equipment Manufacturers and Aftermarket service channels to supply premium-grade, long life radiators, coolers, and full cooling packages into extreme applications all over the world. With our expanding inventory and fabrication space at our Fairfield, Ohio facility, we pride ourselves on having a personal touch, ultra-fast lead times, and one-off custom design capabilities.
For your next vehicle or heavy equipment heat transfer project, call us at (513) 874-5555, email us at sarslan@cincyradiator.com, or visit our website at https://cincyradiator.com/.